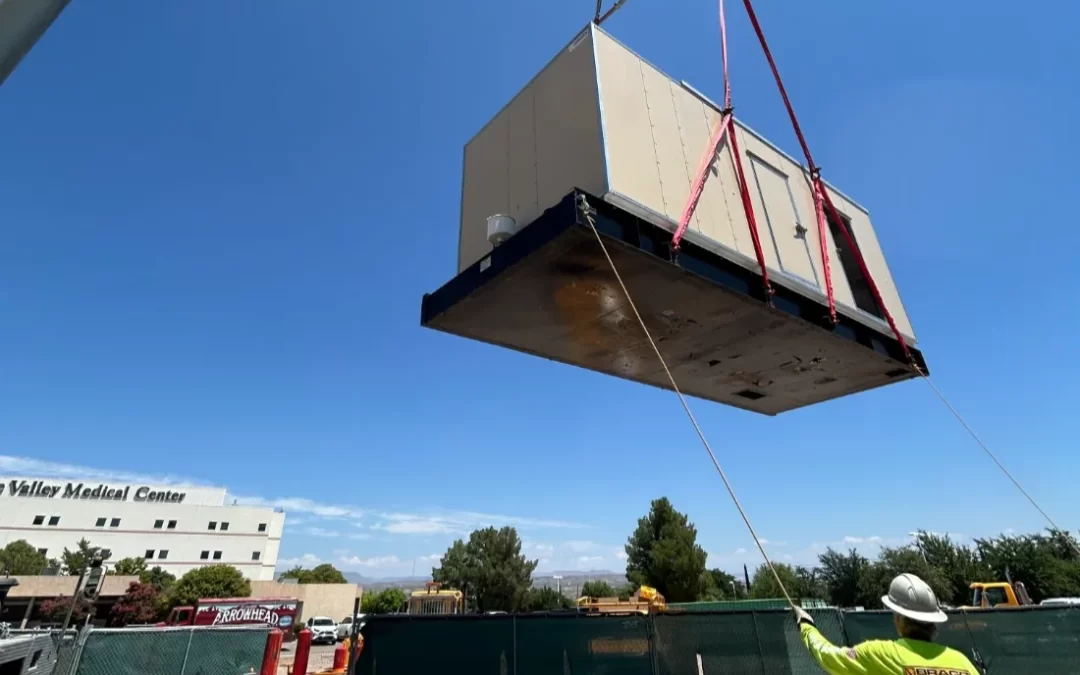
Verde Valley Medical Center Central Plant Expansion
Verde Valley Medical Center’s Central Plant Expansion
Location
Cottonwood, Arizona
Key installations included a new boiler, deaerator tank, and a generator yard enclosed by site walls. The yard housed an 800-gallon diesel tank, a 1,000-gallon belly tank, and a 750-watt generator. Control systems and annunciators were upgraded, and outdated equipment was upgraded.
Three new Automatic Transfer Switches (ATS) were installed, requiring power switchovers in critical patient care areas. These were completed with meticulous coordination to ensure uninterrupted healthcare operations. The result is a modernized central plant with state-of-the-art systems, supporting safe and reliable services across the campus.
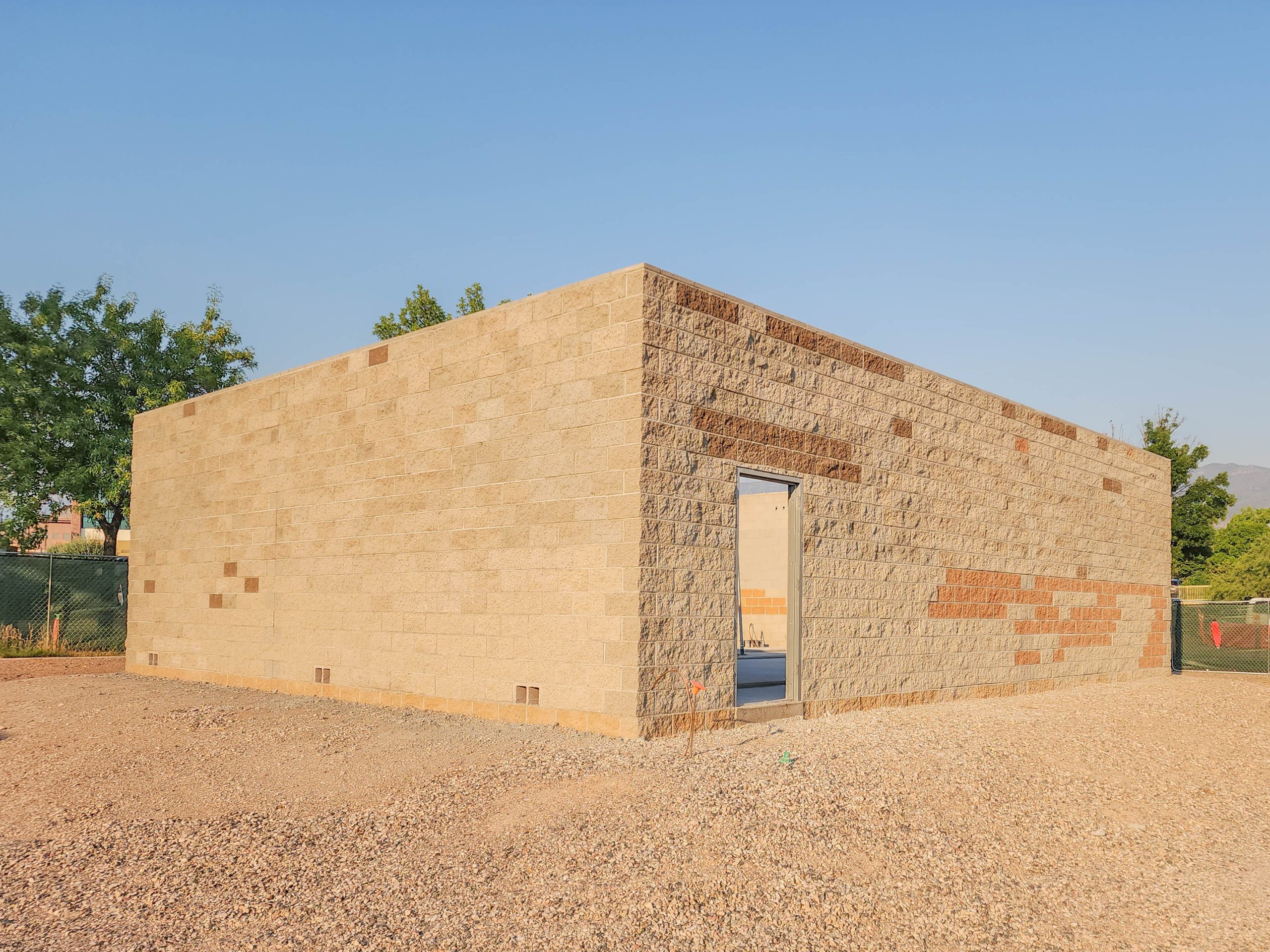
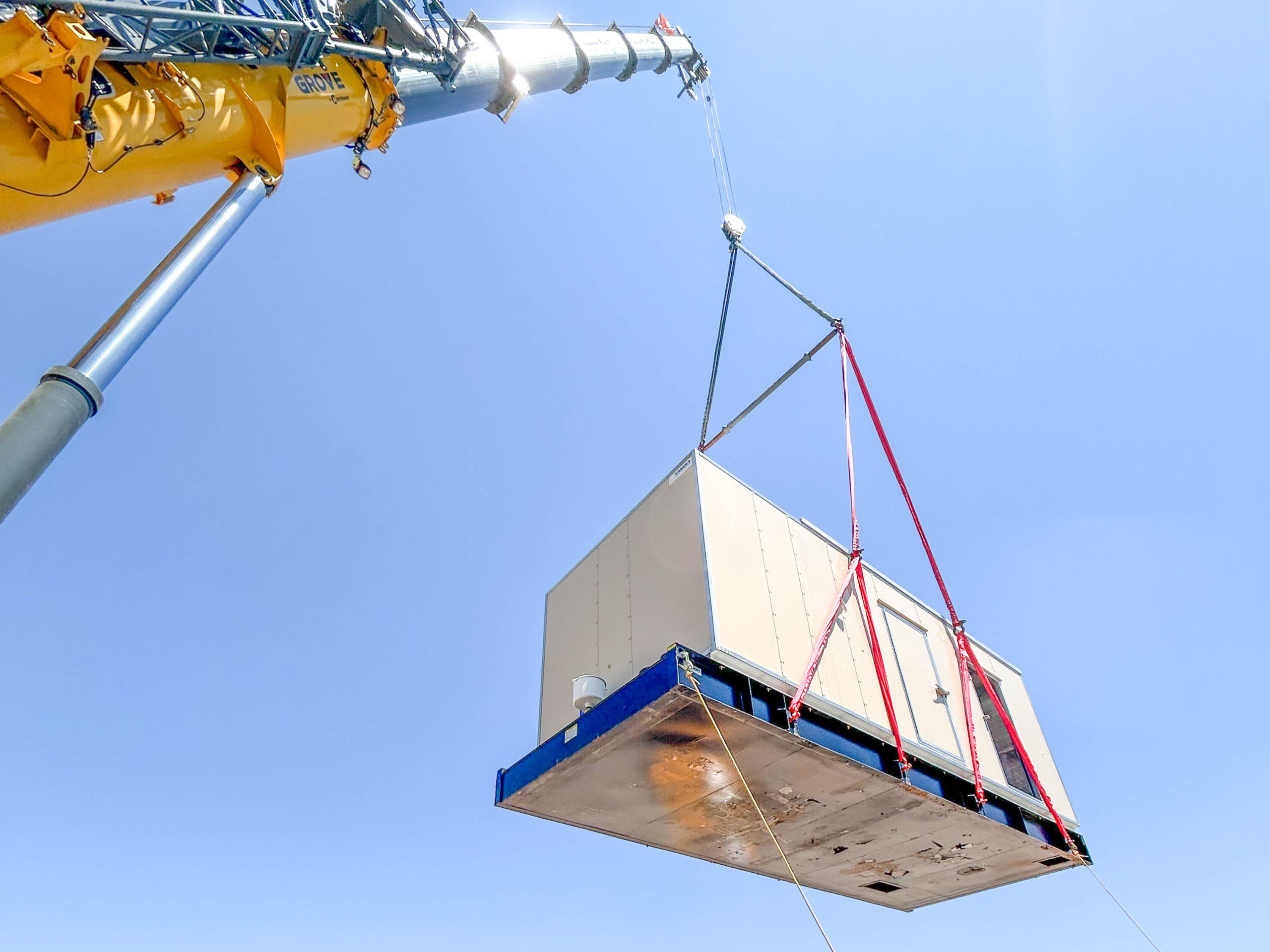
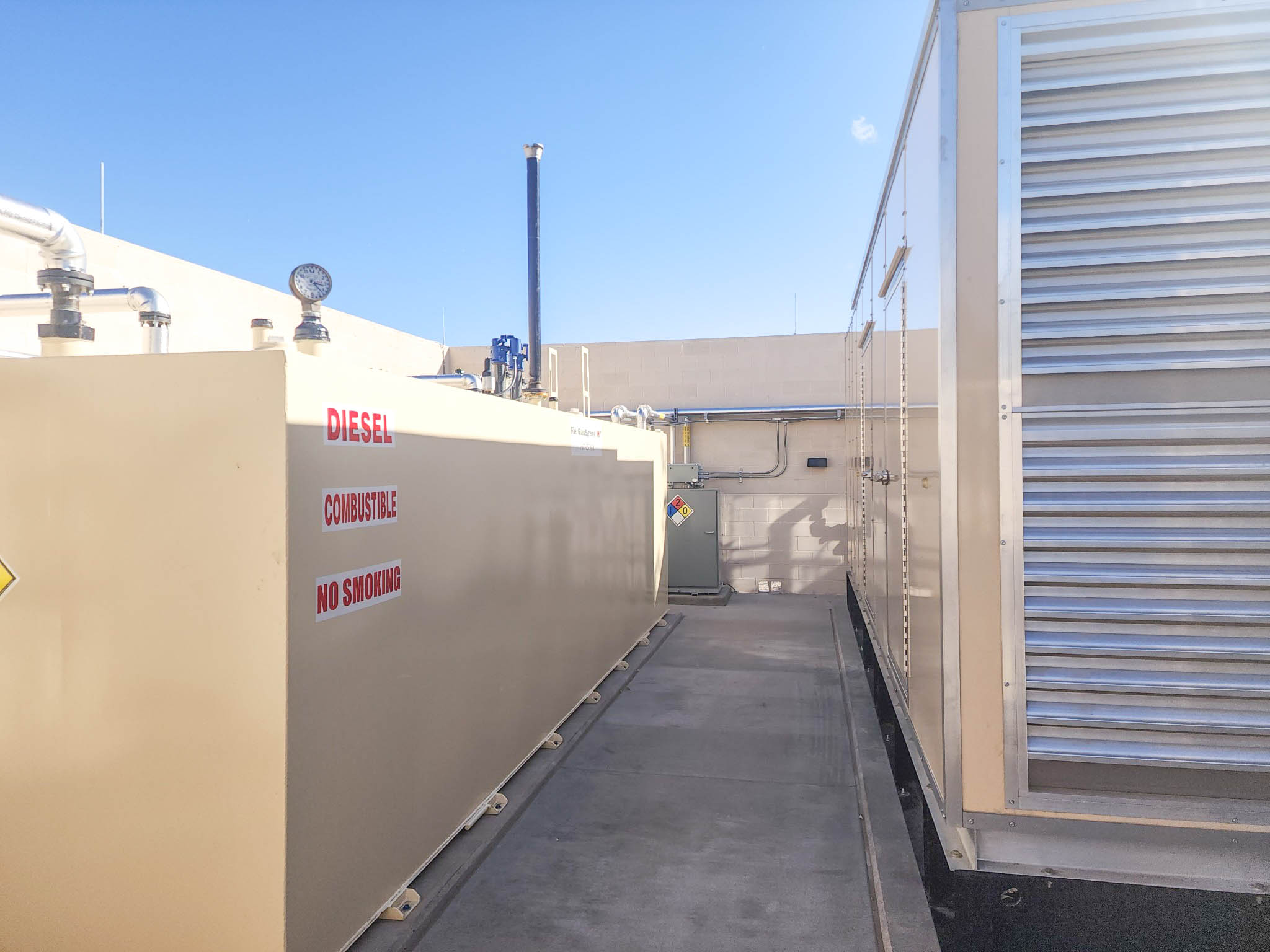